12-Tonne Tank Lifted with 3D Printed Parts
June 08, 2023

Recently, engineers from Ultimaker, Covestro, and the Royal Dutch Navy came together to answer the question, “How Strong are 3D Printed Parts?” Turns out, a plastic 3D-printed part can lift a 12-tonne tank.
Usually, engineers measure a material's strength by using a tensile testing machine. Generally, a small sample print is created and tested under a large force until it snaps. The force projected on the part divided by the surface of the central intersection at the time of breaking will reveal its strength.
While this makes sense to engineers, it often doesn't come across very well to others who may need to see something to understand how it works, so they decided to show an example of just how strong a 3D-printed plastic part could be by lifting something very heavy: a tank.
Now that is a fun experiment!
How They Created the First Prototype Design
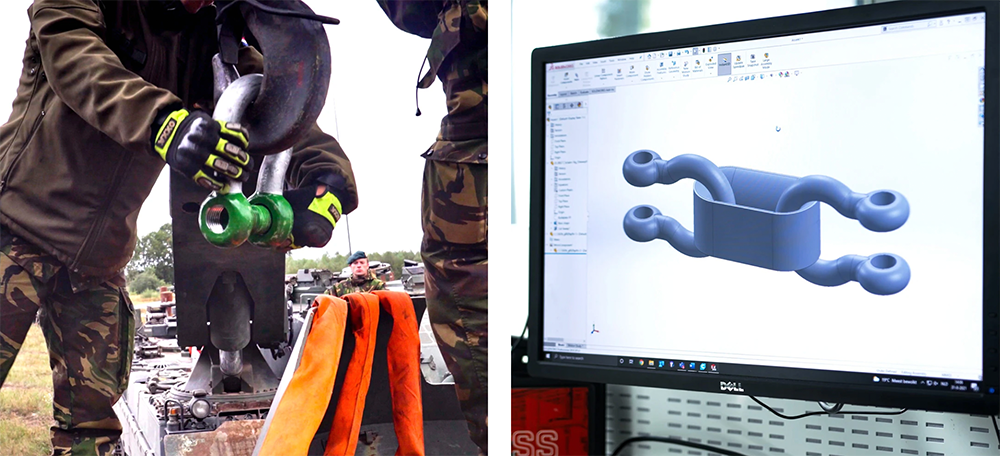
In order to lift a heavy vehicle like a 12-tonne tank using a 3D-printed part, first you need to analyze the hardware available.
The Royal Dutch Navy has a lifting tank that uses two openable steel rings to connect to their crane, and to the cables attached to the vehicle they wanted to lift. An elongated O-shaped link would be the perfect solution to be able to connect these two metal rings and lift the heavy vehicle.
After importing the design of the steel rings into CAD software, Ultimaker Application Engineer, Lars de Jongh was then able to come up with the first initial design for the link they would need. Lars had to work with the design requirements.
First of all, the link needed to have a flat side for a stable 3D print and it needed to be printed with the layer lines in the same direction as the forces projected on the part. On top of that, the 3D-printed part and metal rings' interacting surface needed to be as large as possible to spread forces evenly.
The Ultimaker Marketplace has hundreds of materials to choose from for all kinds of different needs. Each one of them has a unique combination of different properties, which makes it very likely your part will match the set requirements you are trying to work with.
The material needed for this test needed to be extremely strong but it also needed to be able to absorb short-peak forces. They decided to use the Addigy® F1030 CF10 from Covestro which is a nylon-based polymer loaded with carbon fiber and can be printed on the Ultimaker S5 with the CC print core.
Using Simulations to Optimize the Design

It takes much less time to 3D print a solid, 2-kilogram link than it does to produce it with traditional methods. However, the number of iterations necessary to validate the right geometry meant that time was still a factor. That's why they decided the design should be optimized before printing it by using computer simulations
Covestro worked on this project to digitally apply the forces on the design using software that knows the exact physical properties of the carbon fiber nylon material. By running simulations, they were able to identify where the design needed to be adjusted and where material could be removed. This created an optimized design that could lift more weight, while needing less material, resulting in a faster production time with less cost.
Verifying the Simulation

Before lifting a heavy vehicle like a 12-tonne tank, they needed to test the printed part's calculated strength physically to make sure it would work. They created two different designs with two different sizes. The first design was a 1-kilogram link which they estimated could withstand 12 tonnes. The second weighing roughly 2 kilograms was estimated to be able to withstand 38 tonnes.
The Royal Dutch Navy has an on-site industrial tensile tester that is able to project up to an impressive 343 kilonewtons of force on an object. Both the initial and optimized designs were tested for the large and small versions in this experiment.
The optimized design was able to withstand a higher force while weighing a third less. The difference between the tested results and the simulated numbers was also extremely close, being only 1% off on average. This made this workflow accurate and profitable in time-to-market and increased performance.
Lifting Two Different Vehicles with 3D Printed Plastic Parts

After several months of designing, printing, testing, and planning – it was time to finally test these 3D-printed parts in the real world by lifting military vehicles. The parts were taken to the Dutch Army base in the south of the Netherlands where the 13th Light Rhino Brigade assisted in the testing with their armored recovery vehicle. Their Leopard 2 “Buffalo” has a crane mounted on the front and is designed to recover heavy vehicles such as trucks and battle tanks.
First, the 1-kilo link was used to lift a military version of a Mercedes jeep. This vehicle weighs over 2 tonnes. They had no problem lifting it with the link and it was easily lifted.

Next, the 2-kilo solid carbon fiber reinforced nylon link was placed between the M113 armored vehicle and the Buffalo crane. The metal rings were tightened in place and four cables were attached from the lower hook to the vehicle. The crane slowly started to move up, putting the cables and 3D printed part under extreme tension. The 12-tonne tank slowly began to rise and hovered above the ground, hanging from a 3D-printed link! The Buffalo drove around, backward, forward, and even turning around, and the 3D-printed link held up perfectly.
What They Learned From This Test

The project was a great success in not just producing a strong 3D printed part that could lift military vehicles but it was important to see that CAD simulations have come a long way, not just simulating a shape, but giving accurate predictions taking material, and even fiber direction into account. Being able to rely on such tools is a major benefit for engineers as well as the military in general.
While all parts were printed in properly maintained rooms and the materials were not exposed to moisture, there was still a noticeable difference between versions printed in a dry warehouse, and parts printed with deliberately dried spools of filament in a heated, dry print room. Nylon absorbs moisture and this can result in weaker prints. That's why it's very important to know materials' properties and handle them accordingly.
If you are looking for specific materials for projects you are working on, please visit our shop where you can search for materials based on strength, heat resistance, impact resistance, flexibility, food safety and much more.
You can select multiple filters to continue to narrow your search. You can also use the search box at the top of the site to find specific materials.
If you have any questions about 3D printing materials or which 3D printers will be best for your needs, feel free to reach out to us at info@3duniverse.org!